3.3 Chemical active substance testing;
Chemically active substances generally refer to substances with high chemical reactivity (i.e. reactivity), commonly including ions, free atoms, and radicals in solution. Salt mist, SO2, H2S, NO2, ammonia, ozone, etc. have a significant impact on the product.
3.3.1 Salt spray test
Salt mist refers to a dispersion system composed of small droplets containing salt mist in the atmosphere. The content of salt fog is relatively high in the seaside or saline alkali areas, where the seaside is mainly due to the foam generated by the slapping of sea waves, which is then carried into the air by the wind to form atmospheric salt nuclei, thus producing salt fog. The greater the wind speed, the higher the content of salt fog. These salt mist can reach an altitude of over 2000 meters with the rising airflow, and can also drift to land several kilometers away with the wind. The ocean transports approximately 2.72 * 10 ^ 10T of salt nuclei to the land every year, while saline alkali land is a soil containing salt that is blown up and crushed by the wind and brought into the air, rising to the sky with the wind to form dry salt dust or salt mist. According to actual measurements, the amount of salt nuclei measured in Hebei mainland is more than that in Shandong and other coastal areas, but due to dry weather, salt mist may not necessarily form.
failure mechanism
The corrosion of metal materials by salt spray is caused by the chemical reaction between the oxide layer and protective layer of the metal containing chloride ions and the internal metal.
There are three types of failures caused by salt spray, including corrosion, electrical effects, and physical effects. The main reason for corrosion is the ionization of salts in water to form acids and bases, which are prone to electrochemistry; The main reason for the electrical effect is the deposition of salt, which causes damage to electronic equipment, generates conductive layers, and corrodes insulation materials and metals; The physical effect is caused by the interference, jamming, and electrolysis of the moving parts of mechanical components, resulting in surface blistering and detachment.
The coating structure is corroded, and salt mist passes through the aging points of the paint surface and weak points of the process, forming chemical reaction nuclei with the metal structure inside. This is the most significant impact on product failure.
Board level circuit corrosion generally occurs around the edge of the hole ring board. Due to the higher internal stress in this area compared to other locations, the potential of the internal stress location is relatively high. The potential of the internal stress location is low, forming galvanic cell corrosion.
The internal corrosion of the chip is less affected by salt spray, and the chip is basically sealed, which affects the chip's working temperature, humidity, power, working time, etc.
Test standards
The salt spray test mainly refers to IEC 60068-2-11 (GB/T2423.17), MIL-STD-810G Method 509, ASTM B117, ASTM G85, ASTM D610, ISO 4628-3, and ISO 3768. ASTM B117 was the first salt spray test standard, and many countries and industry associations have developed their own salt spray test standards. Now, salt spray testing has been widely adopted by many industries.
The salt spray test is divided into neutral salt spray test (artificial seawater salt spray test and sodium chloride solution salt spray test), acidic salt spray test (acetate spray test and copper accelerated acetate spray test), and alternating salt spray test. Generally, neutral salt spray test is used.
NSS test (neutral salt spray) is applicable to the following surface treatments: electrogalvanizing, hot-dip galvanizing, Dacromet, and various process paints;
The corrosion rate of ASS (acetate mist) is about three times that of NSS; Suitable for final passivation film products such as galvanizing, and various process paints;
The corrosion rate of CASS (steel accelerated acetate mist) is about 8 times that of NSS; Suitable for surface treatment verification of electroplating copper, nickel, and chromium, as well as various process paints.
Alternating salt spray: Neutral salt spray with constant humidity and heat, used for whole machine products with cavities. Through the infiltration of humidity environment, salt spray is not only generated on the surface, but also internally.
The main influencing factors of salt spray test include temperature, humidity, pH value, salt spray concentration, sample placement angle, and solution impurities.
1. Temperature: The test temperature is 35, which has the strongest corrosion impact. The increase in test temperature accelerates the corrosion rate of the product surface. When the temperature increases, the ion migration in the liquid film on the product surface accelerates, and the oxygen diffusion rate also greatly accelerates. If the temperature increases by 10 degrees, the corrosion rate will increase by 2-3 times. But after reaching 35 degrees, the corrosion rate actually weakens with the increase of temperature. This is because under certain conditions, the solubility of oxygen in the solution is inversely proportional to temperature.
2. Humidity: The level of humidity determines the water content in the air. When the humidity is low, the relative corrosion rate of the product is slow; If the humidity is high, the corrosion rate of the product increases exponentially. Under the same temperature conditions, the corrosion rate is directly proportional to the increase in relative temperature.
3. Salt solution concentration: A concentration of 5% is required in the experiment.
4. Sample placement angle: In the salt spray test, the temperature/concentration of the salt solution is constant, and the corrosion effect of the metal is based on the sedimentation of the salt spray. Within a certain angle range, the sample angle will affect the projected area on the horizontal plane, resulting in a greater amount of salt spray deposition. Therefore, the effective test sample should be placed at an angle of 15-45 from the vertical direction.
5. Test time: 24h48h96h Choose based on the working environment and duration of the product, and generally choose a 30 day salt spray test for outdoor products.
3.3.2 Mixed corrosive gas test
The corrosive gases in the air mainly include sulfur dioxide, hydrogen sulfide, nitrogen dioxide, chlorine gas, etc. The sources of corrosive gases mainly include the combustion of mineral fuels, coal, petroleum, and other minerals that contain a considerable amount of sulfur. If these minerals are not treated with sulfur, they will produce a large amount of sulfur dioxide during combustion; Hydrogen sulfide mainly comes from the petrochemical and steel industries, decayed organic matter, sewage, and animal nests. The decayed organic matter decomposes under the action of anaerobic sulfate reducing bacteria to produce hydrogen sulfide gas; Nitrogen dioxide mainly comes from the release of high-temperature combustion processes, such as motor vehicle exhaust and boiler exhaust emissions; Chlorine mainly comes from the pulp and paper industries.
Gas corrosion testing can simulate the potential failure of products in the atmospheric environment and workplace by controlling conditions such as temperature, humidity, and gas concentration, and evaluate the impact of various harmful gases on products.
failure mechanism
Sulfur dioxide:
1. Strong reducing agent, with strong corrosion resistance to general non-metallic surface coatings and non-metallic materials; The corrosion on the surface of metal materials is caused by chemical reactions between the oxide layer and protective layer of the metal containing chloride ions and the internal metal.
2. It forms strong acids and has strong corrosion ability on general non-metallic surface coatings and non-metallic materials.
3. The generated sulfite and sulfuric acid directly damage the oxide film on the surface of metal products, causing various corrosion effects such as electrochemical corrosion.
Hydrogen sulfide:
1. Once H2S dissolves in water, it immediately ionizes, making the water acidic.
2. The aqueous solution of hydrogen sulfide can react with the metal elements in the order of metal activity that are ahead of hydrogen.
3. Hydrogen sulfide has a strong corrosive effect on both copper and silver.
Nitrogen dioxide:
1. Nitrogen dioxide has strong oxidizing properties.
2. It is highly corrosive to general rubber, especially diene rubber such as natural rubber, butadiene rubber, styrene butadiene rubber, etc.
3. Once nitrogen dioxide dissolves in water, it forms nitric acid, which is corrosive to metals.
Chlorine gas:
1. Chlorine has strong oxidizing properties, and it is reduced to chloride, which can penetrate the oxidation protective layer on the metal surface. Chlorine reacts with water to form hydrochloric acid and hypochlorous acid.
2. Metals are not pure substances and have other impurities that can form a primary battery. Active metals are the negative electrode, inactive metals are the positive electrode, and HCl solution is the electrolyte to cause primary battery corrosion.
3. Chlorine can have synergistic effects with hydrogen sulfide and sulfur dioxide.
Test standards
In the early 1990s, professional organizations such as IEC, Telcordia, ASTM, EIA, and ISO began to develop relevant standards and specifications for mixed gas corrosion testing
In gas corrosion tests, copper sheets are usually used as reference specimens, and copper sheet specimens should be subjected to exposure corrosion tests together with experimental samples to verify compliance with various limitations specified in the standard. The weight gain of the copper sample will be used as a measure of this compliance.
IEC 60068-2-60/GB-T 2423.51
1、 Cleaning procedure for copper sheets:
1. Using stainless steel or platinum as the anode, perform cathodic oil removal for 15 to 30 seconds in a 1mol/L sodium hydroxide solution at an electrolytic voltage of 5V to 10V.
2. Rinse with tap water and deionized water
3. Immerse in 10% sulfuric acid solution for activation for 20-30 seconds
4. Rinse with tap water and deionized water
5. Alcohol flushing
6. Hot air drying (approximately 50 ℃)
2、 Test Procedure:
When the test gas does not contain chlorine or the method of measuring chlorine concentration is not disturbed by the test gas, the following procedure should be used:
1. Adjust temperature and humidity
2. Introduce corrosive gas and stabilize it
3. Stabilize temperature, humidity, and gas concentration. (The maximum length should not exceed 24 hours)
4. Inject gas to stabilize it. During the test, the temperature, humidity, and gas concentration should be maintained within the specified range.
5. After the test is completed, stop injecting other gases.
6. Take out the sample.
Note: When measuring chlorine concentration, all chlorine in the test gas should be used as the chlorine concentration (not only chlorine).
When the test gas contains chlorine or the method of measuring chlorine content is disturbed by other test gases, the following procedure should be used:
1. Adjust temperature and humidity
2. Introduce chlorine gas and stabilize it
3. Stabilize temperature, humidity, and chlorine concentration. (The initial concentration of chlorine gas has a high initial chemical reaction and adsorption rate with the test sample, so it should be maintained for at least 2 hours and no longer than 24 hours.)
4. Inject gas to stabilize it, and during the test, the temperature, humidity, and gas concentration (excluding chlorine) should be maintained within the specified range.
5. After the experiment, stop introducing other gases except chlorine gas and measure the chlorine concentration.
6. Take out the sample.
3、 Condition parameters:
Test time optimization: 4d, 7d, 10d, 14d, 21d
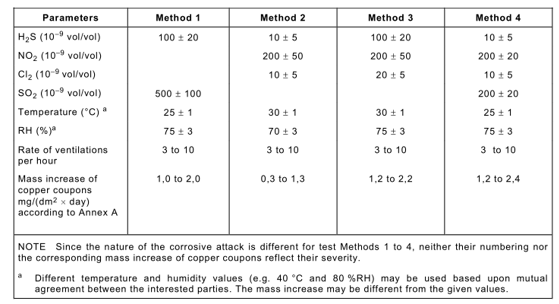
Among them, Method 1 can be used for the pitting corrosion test of the gold clad floating layer. It can also be used to detect surface gold-plated contacts exposed to slightly polluted environments (such as clean telecommunications centers).
Method 2 and Method 4 are applicable to the testing of electrical and electronic products used in moderately corrosive environments, including telecommunications centers, office environments, and industrial instrument and equipment rooms.
Method 3 is suitable for environments with severe corrosion, such as industrial sites.
Telcordia GR-63-CORE
1、 Cleaning procedure for copper sheets:
Cleaning method 1
1. Soak the copper strip in a beaker filled with 2% hot alkaline water solution (pH 7.5-10), and then wash the beaker in an ultrasonic cleaner for 5 to 10 minutes.
2. Remove the copper strip from the solution and rinse it with running tap water for 5 to 15 seconds. Continue immediately to the next step.
3. Hang the copper strip vertically in a solution mixed with one part of concentrated hydrochloric acid and three parts of deionized water, and hold for 2 minutes.
4. Before the surface of the copper strip is dry, immediately place the copper strip in one of the following solutions: a) hang vertically in flowing deionized water for 15 seconds, b) place the copper strip in deionized water and stir for 15 seconds. Immediately place the copper strip in a second cup of deionized water.
5. Before the surface of the copper strip is dry, immediately hang the copper strip vertically in a beaker filled with methanol, and place the beaker in an ultrasonic cleaner for 30 to 60 seconds.
6. Remove the copper strip and immediately blow dry in pure nitrogen or clean air.
After 10 minutes, store the cleaned copper sheet in a glass bottle with a cap.
Cleaning method 2
1. Soak the copper strip in n-hexane solution for 2 minutes, allowing it to hang and drip dry for 10 seconds.
2. Soak the copper sheet in Alphametals Lonco flux 3355-11 (or equivalent solvent) for 15 seconds, allowing for 10 seconds to drip dry.
3. Rinse the copper strip twice with deionized water for 15 seconds each time.
4. Rinse the copper strip with methanol for 15 seconds and dry it.
During the drying process of copper sheets, place them in a glass bottle and leave them open for 10 minutes.
6. After the copper sheet is dried, cover the bottle cap.
The copper sheet needs to be weighed before and after the test. Wait at least 1 hour before weighing to adapt the copper strip to the weighing environment and instrument. Each copper sheet should be weighed at least 3 times, with an error range of 10 for each weighing μ G. If the error range exceeds 10 μ g. The copper sheet needs to be weighed repeatedly until a stable weight is obtained. After weighing the copper sheet, place it in the test chamber and record the weighing value and time. During the experiment, it is allowed to remove copper sheets at appropriate intervals, and a balance time of 30 minutes should be ensured during the repeated weighing process of the copper sheets.
2、 Test Procedure:
1. Place the copper sheet and sample in the test chamber.
2. Introduce Cl2 into the test chamber.
3. Adjust the inlet rate of Cl2 to ensure that the Cl2 concentration meets the requirements, and adjust the air exchange rate to ensure that Cl2
The concentration error is within the required range.
4. Record the concentration value of Cl2.
5. Introduce three gases: NO2, SO2, and H2S.
6. Adjust the inlet rate of NO2, SO2, and H2S to ensure that the three gases meet the requirements, and adjust the air exchange rate to ensure that the concentration error of the three gases is within the specified range.
7. Record the concentration values of NO2, SO2, and H2S gases.
8. Start 10 days of testing