1、 Basic information of the standard:
Standard name: Environmental testing Part 2: Test methods Test Kb: Salt spray, alternating (sodium chloride solution)
Standard number: GB/T 2423.18-2021/IEC 60068-2-52:2017
This standard replaces GB/T 2423.18-2012 'Environmental Testing - Part 2: Test Methods - Test Kb: Salt Spray, Alternating (Sodium Chloride Solution)'
This standard was issued on May 21, 2021 and will be implemented on December 1, 2021.
This standard is under the jurisdiction of TC8 (National Technical Committee for Standardization of Environmental Conditions and Environmental Testing of Electrical and Electronic Products) and is implemented by TC8/SC2 (Climate and Environmental Testing Branch of National Technical Committee for Standardization of Environmental Conditions and Environmental Testing of Electrical and Electronic Products). The competent department is the National Standardization Management Committee.
Scope of this standard: This document describes the application of alternating salt spray testing in components or equipment that can withstand saline atmospheres, as salt can reduce the performance of metallic and/or non-metallic materials.
Test method:
This document is applicable to components or equipment that are resistant to saline atmospheres. During testing, the corresponding severity level is selected based on the degree of tolerance. This document provides 8 test methods:
Test Method 1
A cycle is 7d. One cycle should include spraying the test sample with a salt solution for 2 hours at 35 ° C ± 2K, and then storing it for 6 days and 22 hours under humid and hot conditions at 40 ° C ± 2K and relative humidity (93 ± 3)%. The number of cycles is four (28d).
In the case of manual operation, the transfer time (up to 2 hours) should be included in the humid and hot conditions of 6d22 hours.
Test Method 2
A cycle is 1d. One cycle should include spraying the test sample with a salt solution for 2 hours at 35 ℃ ± 2K, and then storing it for 22 hours under humid and hot conditions at 40 ℃ ± 2K and relative humidity (93 ± 3)%. The number of cycles is three (3d).
In the case of manual operation, the transfer time (up to 2 hours) should be included in the humid and hot conditions of 22 hours.
Test Method 3
A cycle is 7d. One cycle should include spraying the test sample with a salt solution for 2 hours at 35 ° C ± 2K, and then storing it for 22 hours under humid and hot conditions at 40 ° C ± 2K and relative humidity of (93 ± 3)%. Repeat this four times. Then, the test sample is stored in a standard atmosphere of 23 ℃ ± 2K and a relative humidity of (50 ± 5)% for 3 days. The required number of cycles is one (7d).
In the case of manual operation, the transfer time (up to 2 hours) should be included in the humid and hot conditions of 22 hours and the standard atmospheric period of 3 days.
Test Method 4
According to Test Method 3, the required number of cycles is two (14d).
Test Method 5
According to Test Method 3, the required number of cycles is four (28d).
Test Method 6
According to Test Method 3, the required number of cycles is eight (56d).
Test Method 7
A cycle lasts for 8 hours. One cycle should include spraying the test sample with a salt solution for 2 hours at 35 ° C ± 2K, then maintaining it for 4 hours under dry conditions of 60 ° C ± 2K and relative humidity ≤ 30%, and then maintaining it for 2 hours under humid and hot conditions of 50 ° C ± 2K and relative humidity ≥ 95%. The transition time between temperature and humidity (the allowable time to reach the specified temperature and relative humidity after changing the test conditions) should be selected from the following conditions:
——Salt spray to dry conditions: within 30 minutes or within 30 minutes to 60 minutes;
——Drying to humid and hot conditions: within 15 minutes or between 15 and 30 minutes;
——Damp heat to salt spray conditions: within 30 minutes.
These transfer times should be included in the next test condition time, for example, the drying condition time includes the transition time from salt spray to drying conditions. Once the salt spray conditions begin, start spraying the test sample with a salt solution. The recommended number of cycles is 3 (1d), 6 (2d), 12 (4d), 30 (10d), 45 (15d), 60 (20d), 90 (30d), 150 (50d), and 180 (60d)
Test Method 8
A cycle lasts for 8 hours. As per Test Method 7, use acidic salt solution instead of neutral salt solution. The number of cycles should be the same as Test Method 7.
2、 The generation of salt mist environment:
Salt mist refers to a dispersion system composed of small droplets containing salt mist in the atmosphere. The content of salt fog is relatively high in the seaside or saline alkali areas, where the seaside is mainly due to the foam generated by the slapping of sea waves, which is then carried into the air by the wind to form atmospheric salt nuclei, thus producing salt fog. The greater the wind speed, the higher the content of salt fog. These salt mist can reach an altitude of over 2000 meters with the rising airflow, and can also drift to land several kilometers away with the wind. The ocean transports approximately 2.72 * 10 ^ 10T of salt nuclei to the land every year, while saline alkali land is a soil containing salt that is blown up and crushed by the wind and brought into the air, rising to the sky with the wind to form dry salt dust or salt mist. According to actual measurements, the amount of salt nuclei measured in Hebei mainland is more than that in Shandong and other coastal areas, but due to dry weather, salt mist may not necessarily form.
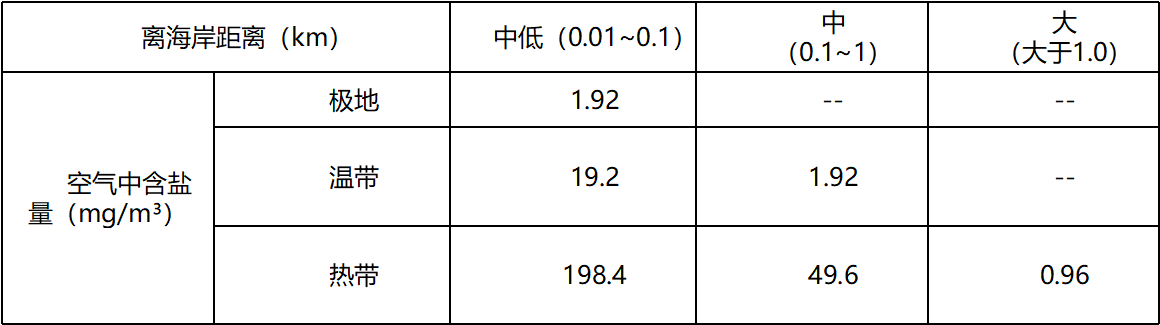
3、 Failure mechanism of salt spray test:
The corrosion of metal materials by salt spray is caused by the chemical reaction between the oxide layer and protective layer of the metal containing chloride ions and the internal metal.
There are three types of failures caused by salt spray: corrosion, electrical effects, and physical effects. The main reason for corrosion is the ionization of salts in water to form acids and bases, which are prone to electrochemistry; The main reason for the electrical effect is the deposition of salt, which causes damage to electronic equipment, generates conductive layers, and corrodes insulation materials and metals; The physical effect is caused by the interference, jamming, and electrolysis of the moving parts of mechanical components, resulting in surface blistering and detachment.
The coating structure is corroded, and salt mist passes through the aging points of the paint surface and weak points of the process, forming chemical reaction nuclei with the metal structure inside. This is the most significant impact on product failure.
Board level circuit corrosion generally occurs around the edge of the hole ring board. Due to the higher internal stress in this area compared to other locations, the potential of the internal stress location is relatively high. The potential of the internal stress location is low, forming galvanic cell corrosion.
The internal corrosion of the chip is less affected by salt spray, and the chip is basically sealed, which affects the chip's working temperature, humidity, power, working time, etc.
4、 ORT salt spray test capability:
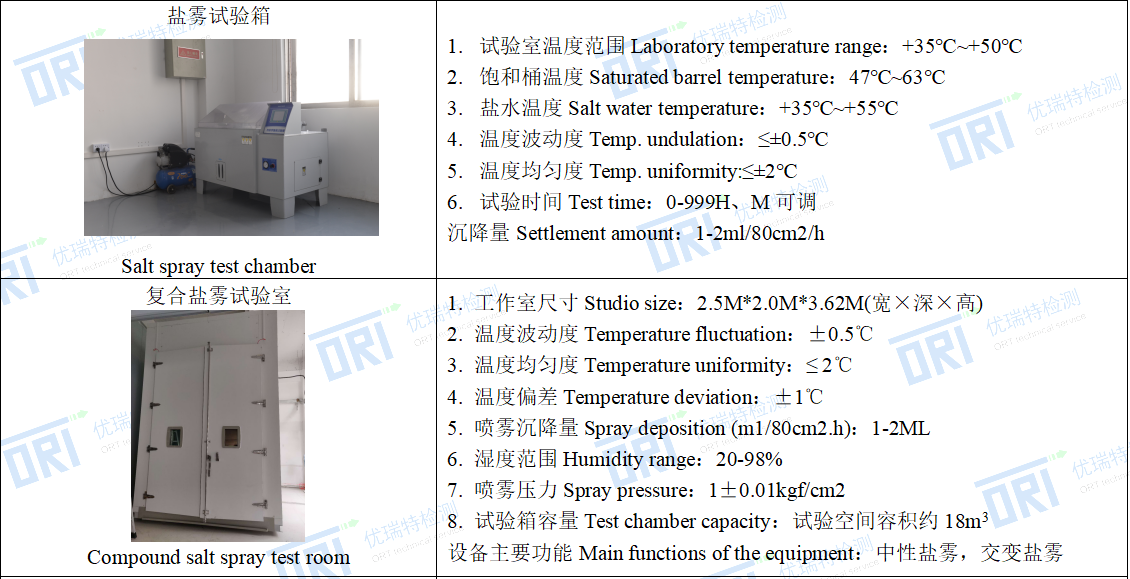
5、 Standard drafting unit:
6、ORT participated in drafting and published standards:
1. GB/T 35774-2017 'Specification for Performance Testing of Transport Packaging Components'
2. GB/T 4857.1-2019 'Basic Testing of Packaging, Transportation, and Packaging Components - Part 1: Marking Methods for Various Parts during Testing'
3. GB/T 4798.1-2019 'Classification of Environmental Conditions - Classification of Environmental Parameter Groups and Classification of Their Severity - Part 1: Storage'
4. GB/T 2421-2020 'Overview and Guidelines for Environmental Testing'
5. GB/T 2423.27-2020 'Environmental Testing - Part 2: Test Methods, Test Methods and Guidelines: Temperature/Low Pressure or Temperature/Humidity/Low Pressure Combined Tests'
6. GB/T 2423.51-2020 'Environmental Testing - Part 2: Test Methods - Test Ke: Flow Mixed Gas Corrosion Test'
7. GB/T 32065.8-2020 Marine Instruments - Environmental Testing Methods - Part 8: Temperature Change Test
8. GB/T 32065.10-2020 Marine Instruments - Environmental Testing Methods - Part 10: Salt Spray Test
9. GB/T 4797.9-2021 Classification of Environmental Conditions - Natural Environmental Conditions - Shock and Vibration Data Measured during Storage, Transportation, and Use
10. GB/T 2423.33-2021 Environmental Testing Part 2: Test Methods Test Kca: High Concentration Sulfur Dioxide Test
11. GB/T 2423.18-2021 Environmental Testing Part 2: Test Methods Test Kb: Salt Spray, Alternating (Sodium Chloride Solution)
12. NB/T 10279-2019 'Wet and Hot Environmental Conditions for Transmission and Transformation Equipment'
13. NB/T 10280-2019 'Wet and Hot Environmental Conditions and Technical Requirements for State Monitoring Devices Used in Power Grids'
14. YZ/T 0174-2020 Technical Requirements for Cold Chain Delivery Insulation Box
15. T/CPF 0012-2020 Guidelines for Testing Small Transport Packages for Express Delivery
16. T/CPF 0011-2020 Guidelines for Testing Electrical Transportation Packaging in E-commerce Logistics