3.1.6 Water test
During use and transportation, the product may be exposed to rain, condensation, and water droplets that fall due to leaks in the natural environment, and in severe cases, it may even be submerged.
The rain test may cause safety accidents due to product short circuits or insulation breakdown, as well as damage to the surface coating of the product, accelerating metal corrosion and reducing the strength of some materials. Products that are not tightly sealed can also penetrate into the interior of the product, resulting in product failure due to expansion.
Rainwater in nature is usually accompanied by wind, and the rainfall speed and vertical inclination angle of the rain can also be different, which poses a challenge to the environmental adaptability of the product.
failure mechanism
Rain exposure mainly refers to the climatic conditions that occur to verify the waterproof ability of products under specific climatic conditions. The main failures caused by it are as follows:
1. Electrical short circuit 2. Material deformation
Environmental profile
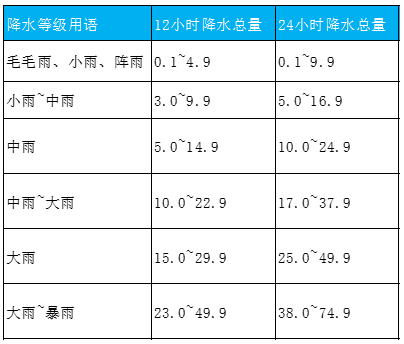
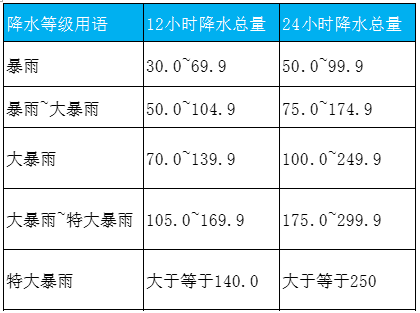
Test standards
The water test mainly refers to the IEC60068-2-18 (GB/T2423.38) MIL-STD-810 Method 506 IEC 60529 (GB 4208) standard. The introduction of the US military standard test method is quite detailed and can be used as a reference book. The specific method for civilian products is mainly IEC. The recommended values for the severity and duration of the test are as follows.
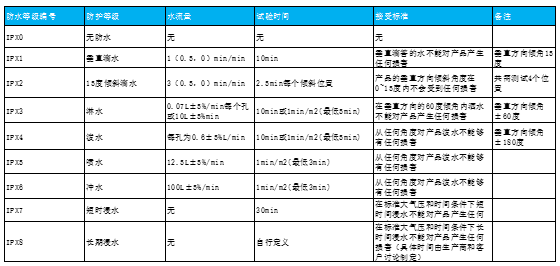
3.1.8 Solar radiation
The Earth rotates once, and the vast majority of regions are subjected to solar radiation, which can be said to accompany our daily lives.
The spectrum produced by solar radiation is divided into visible light, infrared, and ultraviolet, and some materials may undergo aging and degradation after exposure to radiation.
failure mechanism
After the appearance of sunlight, the temperature in the corresponding area begins to rise, while after the disappearance of sunlight, the temperature gradually decreases at night, which is caused by solar radiation.
The impact of solar radiation on products is mainly caused by heating effects and optical chemical effects. The heating effect is mainly generated by the infrared spectrum in the solar radiation. Mainly causing short-term high temperature and local overheating of the product, causing the failure of some temperature sensitive components, mechanical damage to structural materials, and overheating damage to insulation materials. The photochemical effect is mainly generated by the ultraviolet spectrum in solar radiation, which provides enough light energy to stimulate organic material molecules to break, degrade, or interact, leading to material aging and deterioration. When solar radiation is combined with climate factors such as temperature and humidity, its damage is more pronounced. The most common types of damage are surface damage such as deformation, discoloration, loss of gloss, pulverization, and cracking. At the same time, their inherent mechanical and electrical properties will also decrease, resulting in a decrease in the material's useful value or even scrapping.
For aging and degradation, we usually see pigment fading and material aging. Indoor exposure to less light leads to slower degradation and aging, while outdoor exposure to more light leads to faster degradation and aging. The energy of solar radiation is related to the geographic latitude, altitude, and time changes. The physical quantity that measures the strength of solar radiation is solar irradiance, in units of w/m2, which represents the energy absorbed per unit time area when sunlight hits the surface.
The degree and type of degradation of paint coatings depend on the spectral sensitivity of the resin. Different wavelengths of light have different destructive effects. Each resin has different spectral sensitivity, which determines whether a resin is sensitive to short wavelength, long wavelength, or both.
Resin used in coatings mainly consists of one or several functional groups (such as C-CC-HC-O) from polyester resin, amino resin, alkyd resin, and propylene resin. The corresponding threshold wavelength range of the functional groups is 231-376nm, which corresponds to the short wavelength ultraviolet band in sunlight.
If temperature and humidity stress are added to the coating, it will accelerate the entire aging process.
Test standards
Solar radiation mainly refers to IEC 60068-2-5 (GB/T2423.24) IEC 60068-2-9 (GB/T2424.14) (old version guidelines) MIL-STD-810G Method 505ISO 4892-1-4 (GB/T 16422.1-4).
light source
1. Metal halide lamp: also known as metal halide lamp, using metal halide to provide a spectral energy distribution that is very similar to direct and scattered light. The light source distribution of metal halides is very similar to the sunlight received on the Earth's surface, but due to the large scale of metal halide lamps, they are mainly suitable for outdoor products and larger modules for testing;
2. Xenon lamp: Xenon arc lamp can simulate a complete spectrum of all sunlight, including ultraviolet, visible, and infrared spectra. However, the energy distribution of xenon lamps is different from that of sunlight, so filters need to be used to filter the light on a certain frequency band to meet the corresponding usage. However, it is also because it can simulate natural light in multiple scenarios, such as sunlight shining through the atmosphere onto glass, and then simulating the illumination of scenes such as the car interior by adjusting temperature and humidity; So currently, the preferred method for conducting light aging tests is to conduct xenon lamp aging tests;
3. UV fluorescent lamp: UV lamp is actually a lamp source with a wavelength of 254nm. Due to the addition of phosphorus coexisting compounds, it is converted into longer wavelengths. The energy distribution of UV lamp depends on the emission spectrum of phosphorus coexisting products and the diffusion of glass tubes. UV lamps mainly include UVA, UVB, and a small amount of UVC. Your exposure application determines which type of UV lamp should be used.
UVA-340: Provides the best UV simulation for sunlight. UVA-351: Provides the best simulation of the ultraviolet part of sunlight passing through glass.
UVB-313EL: Short wave ultraviolet below 295nm, widely used for long-term durability aging of coatings such as automobiles.
4. Carbon arc lamp: An ancient technology that was originally a light source for artificial simulation of light aging, but gradually replaced by the above light source due to the significant difference in spectrum and energy compared to sunlight.
Reference test
Solar radiation conditions of a certain mobile phone manufacturer
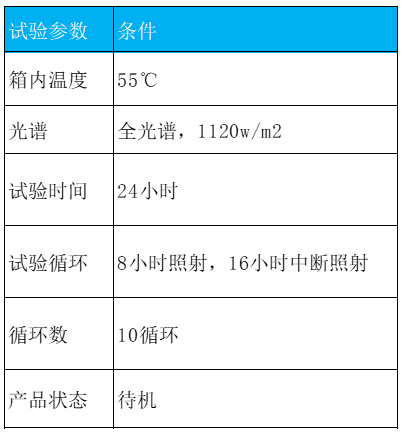
Solar radiation conditions of a certain commercial vehicle
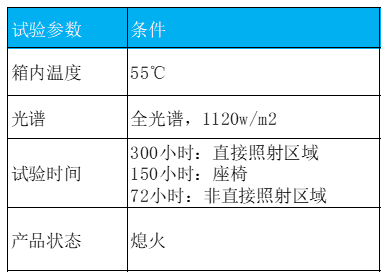
Outdoor enameled wire
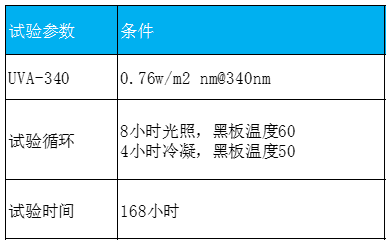
Outdoor metal coating aging conditions
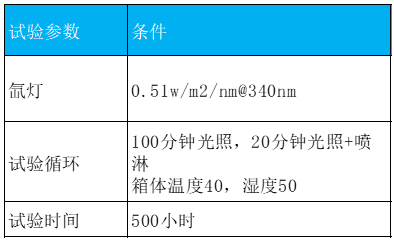
Indoor ink aging conditions
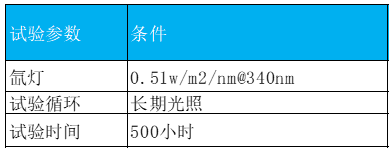
3.1.9 Low pressure test
The atmospheric pressure depends on the altitude. As the altitude increases, the atmospheric pressure gradually decreases and the atmosphere becomes thinner. When the altitude approaches 5.5km, the atmospheric pressure drops to half of the standard atmospheric pressure at sea level; The atmospheric pressure near 16km is 1/10 of the standard sea level value; The atmospheric pressure near 31km is 1/100 of the standard sea level value.
There are quite large areas on the Earth's surface with higher terrain, with about 50% of China's area exceeding 1000m and about 25% exceeding 2000m. The pressure in areas with higher terrain is lower than that in coastal areas. The decrease in air pressure will inevitably have an impact on the electrical and electronic products and airborne equipment used in plateau areas. For aviation products, due to the fact that aircraft must fly at least a few thousand meters, usually at or above ten thousand meters, and up to a maximum of 30 kilometers, airborne equipment will withstand lower atmospheric pressure.
failure mechanism
The impact of low air pressure on sealing products: The impact of low air pressure on sealing products is mainly due to the pressure difference caused by changes in atmospheric pressure. The pressure difference causes a force from high pressure to low pressure. Under this force, the gas flows to achieve equilibrium. For sealed products, the outer shell will withstand this force. This force can cause deformation of the shell and rupture of the sealing element, resulting in product failure.
The impact on heat dissipation: The temperature rise of the heat dissipation product increases with the decrease of atmospheric pressure. A considerable portion of electrical and electronic products are heating products, such as motors, transformers, contactors, resistors, etc. These products require a portion of electrical energy to be converted into thermal energy during use, which will generate heat and increase the temperature. The temperature of the product increases due to heating, and this part of the temperature increase is called temperature rise. The temperature rise of heat dissipation products increases with the decrease of atmospheric pressure and increases with the increase of sea level. Causes phenomena such as decreased performance or unstable operation of the product.
The impact on electrical performance: An increase in sea level and a decrease in air pressure will also have an impact on the electrical performance of electrical and electronic products. Especially for equipment using air as the insulation medium, the impact of low air pressure on the equipment is more significant. Under normal atmospheric conditions, air can be a good insulation medium, and many electrical products use air as the insulation medium. When these products are used in high altitude areas or as airborne equipment, due to the decrease in atmospheric pressure, partial discharge phenomena often occur near electrodes with strong electric fields, known as corona. More seriously, sometimes air gap breakdown occurs. This means that the normal working state of the device is disrupted.
Under low atmospheric pressure, especially with high temperature conditions, the dielectric strength of the gas significantly decreases, that is, the corona initiation voltage and breakdown voltage significantly decrease, thereby increasing the risk of arc surface discharge or corona discharge.
Test purpose
Due to the decrease in atmospheric pressure, the mechanical and electrical properties of the product are greatly affected, sometimes leading to product damage. Due to the increase in altitude, the decrease in atmospheric pressure, the decrease in atmospheric density, and the thinning of the air. Within the height range we are considering (below 3000 meters), the average free path of molecules in the air is still very small, and the atmosphere can still be regarded as a continuous medium fluid. The flow and thermodynamic characteristics of air follow the same physical laws under low pressure conditions as under normal atmospheric conditions. However, compared to normal atmospheric conditions, products are affected differently by low-pressure conditions, such as heat dissipation. From this, it can be seen that under low pressure conditions, the proportion of radiative heat dissipation increases, while the proportion of convective heat dissipation decreases. In addition, due to the decrease in atmospheric density, the surrounding area of the heat dissipation product will also change. The impact of low air pressure on products cannot be simulated under normal atmospheric conditions, therefore a low air pressure test must be conducted.
Test standards
GB2421-1989 'Basic Environmental Testing Regulations for Electrical and Electronic Products - General Principles'
GB2423.21-1991 'Basic Environmental Testing Procedures for Electrical and Electronic Products - Test M: Low Pressure Test Method'
GB/T2423.25-1992 'Basic Environmental Testing Procedures for Electrical and Electronic Products - Test Z/AM: Low Temperature/Low Air Pressure Comprehensive Test Method'
GB/T2423.26-1992 'Basic Environmental Testing Procedures for Electrical and Electronic Products - Test Z/BM: High Temperature/Low Pressure Comprehensive Test Method'
GB2423.27-2005 'Basic Environmental Testing Procedures for Electrical and Electronic Products - Test Z/AMD: Continuous Comprehensive Test Method for Low Temperature/Low Air Pressure/Damp Heat'
GB/T2424.15-1992 'Basic Environmental Testing Procedures for Electrical and Electronic Products - Guidelines for Temperature/Low Air Pressure Comprehensive Testing'
GJB150.2-86 'Environmental Test Methods for Military Equipment - Low Pressure (Altitude) Test'
In GB/T2424.15-1992 'Basic Environmental Testing Regulations for Electrical and Electronic Products - Guidelines for Temperature/Low Air Pressure Comprehensive Testing', the scope of application of temperature and low air pressure, as well as the comprehensive impact testing equipment, are mainly elaborated.
In GB/T2423.25-1992 'Basic Environmental Testing Regulations for Electrical and Electronic Products - Test Z/AM: Low Temperature/Low Air Pressure Comprehensive Test Method' and GB/T2423.26-1992 'Basic Environmental Testing Regulations for Electrical and Electronic Products - Test Z/BM: High Temperature/Low Air Pressure Comprehensive Test Method', specific specifications are provided for the test method, severity level, test purpose, and condition test.
According to GB/T2423.25-1992 'Basic Environmental Testing Procedures for Electrical and Electronic Products - Test Z/AM: Low Temperature/Low Air Pressure Comprehensive Test Method':
1.2.2 Test method: Only one heat dissipation test sample can be tested at a time, and the test samples should generally be tested in a test chamber without forced air circulation in accordance with GB2423.1.
3.2.2 If the test sample needs to work during the testing process, it should be tested to ensure that the test sample can work normally. Then, while maintaining the temperature at the specified value, lower the pressure of the test chamber to the test pressure specified in the relevant standards. Maintain this temperature and pressure condition for the specified time.
In the experiment, it is necessary to distinguish between heat dissipation and non heat dissipation test samples. The following figure shows the standard test profile:

The severity level is also specified in the standard, and the following table shows a set of temperature, pressure, and duration values:
温度℃ | 气压 KPa | 对应高度 m | 持续时间 h |
-55 | 4 | 22100 | 2 |
-55 | 15 | 13600 | 2 |
-55 | 25 | 10400 | 2 |
-55 | 40 | 7150 | 2 |
-40 | 55 | 4850 | 2,16 |
-25 | 55 | 4850 | 2,16 |
-40 | 70 | 3000 | 2,16 |
Similarly, in GB/T2423.26-1992 'Basic Environmental Testing Procedures for Electrical and Electronic Products - Test Z/BM: High Temperature/Low Air Pressure Comprehensive Test Method':
1.2.3 Test method: Only one heat dissipation test sample can be tested at a time, and the test samples should generally be tested in a test chamber without forced air circulation in accordance with GB2423.1.
3.2.2 If the test sample needs to work during the testing process, it should be tested to ensure that the test sample can work normally. Then, while maintaining the temperature at the specified value, lower the pressure of the test chamber to the test pressure specified in the relevant standards. Maintain this temperature and pressure condition for the specified time.
In the experiment, it is necessary to distinguish between heat dissipation and non heat dissipation test samples, and the severity level is also specified in the standard. The following table shows a set of temperature, pressure, and duration values:
温度℃ | 气压 KPa | 对应高度 m | 持续时间 h |
155 | 4 | 22100 | 2 |
85 | 4 | 22100 | 2 |
155 | 15 | 10400 | 2 |
85 | 15 | 13600 | 2 |
55 | 15 | 13600 | 2 |
55 | 25 | 10400 | 2 |
55 | 40 | 7150 | 2 |
55 | 55 | 4850 | 2,16 |
40 | 55 | 4850 | 2 |
55 | 70 | 3000 | 2,16 |