1、 Basic information of the standard:
Standard name: Environmental testing Part 2: Test methods Test Ke: Flow mixed gas corrosion test
Standard number: GB/T 2423.51-2020/IEC 60068-2-60: 2015
This section replaces GB/T2423.51-2012 'Environmental Testing - Part 2: Test Methods - Test Ke: Flow Mixed Gas Corrosion Test'.
This section was released on June 2, 2020 and implemented on December 1, 2020.
This part is under the jurisdiction of TC8 (National Technical Committee for Standardization of Environmental Conditions and Environmental Testing of Electrical and Electronic Products) and is executed by TC8/SC2 (Climate and Environmental Testing Branch of National Technical Committee for Standardization of Environmental Conditions and Environmental Testing of Electrical and Electronic Products). The competent department is the National Standardization Management Committee.
Scope of this standard:
This part of GB/T2423 is used to determine the corrosion impact of indoor environments for work and storage on electrical and electronic product components, equipment, and materials, especially contact points and connectors. Contact points and connectors can be evaluated as individual components, assembled into a component, or assembled into a complete equipment.
The test methods provided in this section are helpful for comparing and selecting materials, manufacturing processes, and component designs in terms of corrosion resistance.
Severity level:
The severity level of the trial test is specified by relevant specifications and depends on the following factors:
——- Test method (selected from Table 1);
——- Test time.
The preferred test time is 4d, 7d, 10d, 14d, and 21d.
There are four test methods, and their test parameters are shown in Table 1. The application of each test method is as follows:
The use of different test methods:
Although copper is considered a good monitoring material, in general, the corrosion weight gain of copper samples treated using the test methods specified in this section is not related to the corrosion of other metal samples.
Test method 1 can be used for pitting corrosion testing of gold coating. For open exposed gold coated surfaces, the test time should be 10 days. Test method 1 can also be used to detect surface gold-plated contacts exposed to slightly polluted environments (such as' clean 'telecommunications centers), with a suitable test time of 10 to 21 days.
Test methods 2 and 4 are applicable to the detection of electrical and electronic products used in moderately corrosive environments, including telecommunications centers, most office environments, and some industrial instrument and equipment rooms. The main corrosion mechanism of the gold coating in these environments is pore corrosion.
Test method 3 is suitable for environments with severe corrosion, such as industrial instrument equipment rooms and other industrial locations. The gold covering layer is prone to pitting and fissure corrosion in these environments.
For Test Method 2, Test Method 3, and Test Method 4, the test time of 4-7 days is applicable to the appearance evaluation of the covering layer system, the test time of 4-10 days is applicable to the evaluation of products with short lifespan, and the test time of 7-21 days is applicable to the evaluation of products with high requirements for reliability and lifespan.
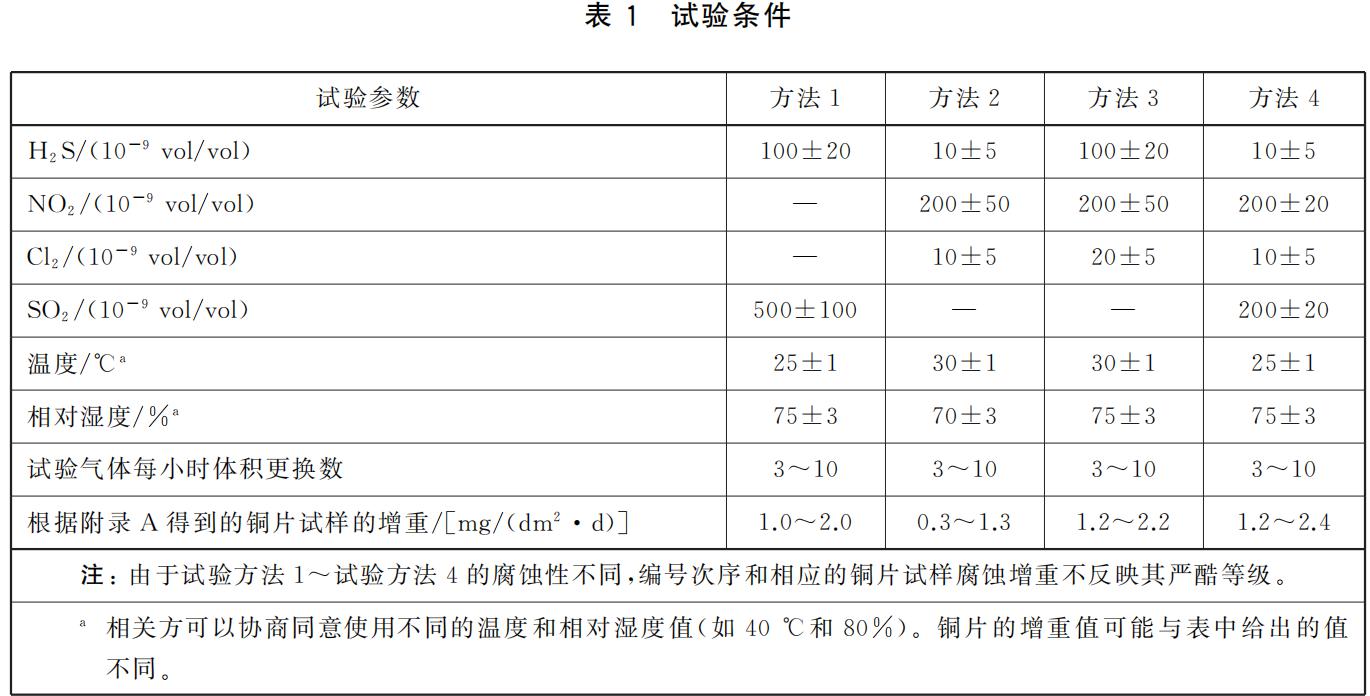
Test sample:
The relevant product specifications should determine the state of the test sample during the testing period, such as whether the connection is connected or not, whether the switch is open or closed, running or under load.
During the operation or load state of the heat dissipation test sample, the temperature and relative humidity of the working space should be maintained within the specified range.
When the test sample is placed in the test chamber, the state of the test sample and the chamber should not cause condensation on the surface of the test sample.
The total volume of the test sample should not exceed 10% of the volume of the entire workspace. If it exceeds 10%, the amount exceeding 10% should be included in the test report.
The total surface area of the test sample should not exceed 10% of the surface area of the entire workspace. If it exceeds 10%, the amount exceeding 10% should be included in the test report.
The minimum spacing between test samples shall not be less than 10mm to avoid affecting uniform airflow.
Corrosion monitoring materials:
The copper sample is tested together with the test sample as a corrosion monitoring material to verify the consistency of the test conditions.
The copper sample shall be prepared according to Appendix A, with a minimum of 5 pieces. During the test, it shall be exposed together with the test sample, and the weight increase of the copper sample during the test shall be measured using a balance with a resolution of 0.01mg, as a measure of corrosion degree and a monitoring standard for test reproducibility and repeatability.
In addition to copper specimens, other materials such as gold plated specimens or other specimens can also be used as corrosion monitoring materials.
Test Procedure 1:
When the test gas does not contain chlorine (Method 1) or the method for measuring chlorine concentration is not affected by other gases in the test gas, the following procedure should be used:
——After the specified temperature stabilizes, start injecting moist air to stabilize and adjust the temperature and humidity to avoid condensation on the inner walls of the studio and test samples.
——- Start introducing corrosive gases into the moist air and stabilizing them.
——- Measure and regulate gas concentration and stabilize it; When measuring the concentration of chlorine, use all chlorine in the test gas (not just chlorine Cl2) as the chlorine concentration; The chlorine in the test gas should only be filled in the form of chlorine Cl2.
——- Place test samples and corrosion monitoring materials specified in 7.3. The copper sample should be exposed together with the test sample in the first 4 days of the test period. If necessary, the copper sample can be exposed for an additional 4 days during the test period and this should be included in the test report. The test samples and corrosion monitoring materials should be evenly distributed in the workspace, and should not come into contact or obstruct the test gas. The state of the test samples should comply with relevant specifications (such as connected/disconnected, electrical load or operation). The test time should be calculated from this point onwards.
——- Stable test conditions may take some time; If necessary, temperature, humidity, and gas concentration can be measured and adjusted; During the adjustment process, any excessive gas concentration should be avoided, and the maximum time for adjustment and stability should not exceed 24 hours.
——- During the test, the temperature, humidity, and gas concentration should be maintained within the specified range; During the test, it is allowed to open the test chamber. The number of times to open the box should be limited. If the test duration is less than 4 days, it is not allowed to open the box; The test duration is 4d~10d, and it is allowed to open the box once; If the test duration exceeds 10 days, it is allowed to open the box once a week; The duration of unpacking is limited to the time required to collect and place test samples or corrosion monitoring materials.
——After the test is completed, remove the test samples and corrosion monitoring materials.
Test Procedure 2:
When the test gas contains chlorine (Method 2, Method 3, Method 4) or the method for measuring chlorine content is disturbed by other gases in the test gas, the following procedure should be used:
——After the specified temperature stabilizes, start injecting moist air to stabilize and adjust the temperature and humidity to avoid condensation on the inner walls of the studio and test samples.
——- Start introducing chlorine gas into the moist air and stabilize it.
——Measure and adjust the chlorine concentration and stabilize it.
——- Place test samples and corrosion monitoring materials specified in 7.3; The copper sample should be exposed together with the test sample in the first 4 days of the test period. If necessary, the copper sample can be exposed for an additional 4 days during the test period and this should be included in the test report. The test samples and corrosion monitoring materials should be evenly distributed in the workspace, and should not come into contact or obstruct the test gas. The state of the test samples should comply with relevant specifications (such as connected/disconnected, electrical load or operation).
——It may take some time to stabilize the temperature, humidity, and chlorine concentration, as chlorine has a high initial chemical reaction and adsorption rate on the surface of the test sample; If necessary, the concentration of chlorine can be measured and adjusted; During the adjustment process, any excessive gas concentration should be avoided, and the adjusted chlorine concentration should be stable for at least 2 hours; The maximum time for adjustment and stability should not exceed 24 hours.
——- Start injecting other gases and stabilizing them, if necessary, measure and adjust temperature, humidity, and gas concentration (excluding chlorine); During the adjustment process, any excessive gas concentration should be avoided, and the maximum time for adjustment and stability should not exceed 24 hours; Test time from
Calculate when all gases are introduced.
——During the test, the temperature, humidity, and gas concentration should be maintained within the specified range, but the chlorine concentration cannot be controlled. The method to ensure that the chlorine concentration is within the specified range is to measure the chlorine content according to regulations after the test is completed; During the test, it is allowed to open the test chamber.
The number of times to open the box should be limited. If the test duration is less than 4 days, it is not allowed to open the box; The test duration is 4d~10d, and it is allowed to open the box once; If the test duration exceeds 10 days, it is allowed to open the box once a week; The duration of unpacking is limited to the time required to collect and place test samples or corrosion monitoring materials.
——After the experiment is completed, in addition to continuing to inject chlorine gas, stop injecting other gases and wait for sufficient time to allow other gases to be discharged from the test chamber, in order to avoid affecting the analysis of chlorine to the greatest extent possible.
——To ensure the effectiveness of the experiment, the measured chlorine concentration should be within the specified range.
——- Take out test samples and corrosion monitoring materials.
The test samples should be visually, dimensionally, and functionally inspected in accordance with relevant specifications.
The relevant specifications should provide a basis for whether the test sample has passed the test.
2、 Failure mechanism
The reason why corrosive atmospheres have the ability to corrode products or materials is closely related to the various atmospheric pollutants they contain.
Atmospheric pollutants are a triggering environmental factor. The most important atmospheric pollutants include sulfur dioxide, carbon monoxide, and fine dust. Sulfur pollutants are an important part of atmospheric pollution, mainly from the combustion of mineral fuels, with high chemical activity. Dust in atmospheric pollutants is most easily detected, including polytype dust and chemically active dust. The atmospheric pollutants and their approximate concentration range are shown in the table below. Cities, industrial zones, and certain military activities are the causes of atmospheric pollution.
Table 1: Typical Air Pollutants
pollutant | Typical concentration/ppm | pollutant | Typical concentration/ppm |
sulfur dioxide | 0.005~2.0 | carbon monoxide | 0.1~100 |
hydrosulfide | 0.001~0.003 | hydrocarbons | 0.1~40 |
nitric oxide | 0.010~0.400 | dust | (10~200)(μg/m³) |
nitrogen dioxide | 0.020~0.030 | / | / |
Table 2: Material failure modes and mechanisms caused by atmospheric pollutants
material | effect | mechanization |
metal | Surface damage, loss of gloss, corrosion | Chemical reactions of SO2 and other acidic gases |
paint | Fading, cracking, softening | Effect of SO2 and H2H viscous particles |
leather | Embrittlement, surface differentiation, reduced tensile strength | The action of acidic gases such as SO2 |
textile | Spots appear, resulting in a decrease in tensile strength | The action of acidic gases such as SO2 |
rubber | Embrittlement, looseness, elastic loss, cracks | Action of O2 and O3 |
ceramics | Loss of surface gloss and decrease in reflectivity | Acid gas action |
Silver electric contact point | Surface discoloration, production of black oxide film, reduced conductivity | Interaction between SO2 and other acidic gases |
3、 Drafting unit of this standard:
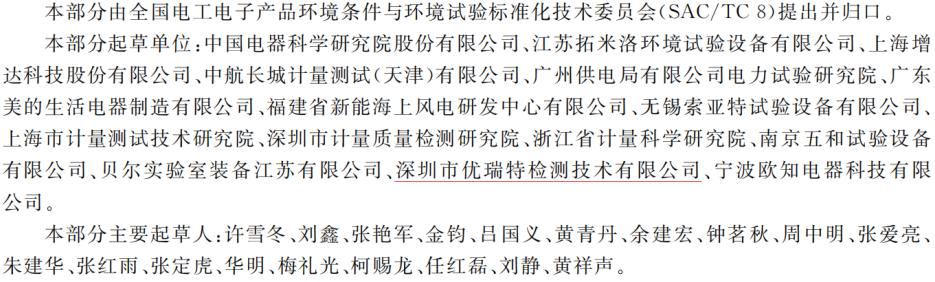
4、ORT participated in drafting and published standards:
1. GB/T 35774-2017 'Specification for Performance Testing of Transport Packaging Components'
2. GB/T 4857.1-2019 'Basic Testing of Packaging, Transportation, and Packaging Components - Part 1: Marking Methods for Various Parts during Testing'
3. GB/T 4798.1-2019 'Classification of Environmental Conditions - Classification of Environmental Parameter Groups and Classification of Their Severity - Part 1: Storage'
4. GB/T 2421-2020 'Overview and Guidelines for Environmental Testing'
5. GB/T 2423.27-2020 'Environmental Testing - Part 2: Test Methods, Test Methods and Guidelines: Temperature/Low Pressure or Temperature/Humidity/Low Pressure Combined Tests'
6. GB/T 2423.51-2020 'Environmental Testing - Part 2: Test Methods - Test Ke: Flow Mixed Gas Corrosion Test'
7. GB/T 32065.8-2020 Marine Instruments - Environmental Testing Methods - Part 8: Temperature Change Test
8. GB/T 32065.10-2020 Marine Instruments - Environmental Testing Methods - Part 10: Salt Spray Test
9. GB/T 4797.9-2021 Classification of Environmental Conditions - Natural Environmental Conditions - Shock and Vibration Data Measured during Storage, Transportation, and Use
10. GB/T 2423.33-2021 Environmental Testing Part 2: Test Methods Test Kca: High Concentration Sulfur Dioxide Test
11. GB/T 2423.18-2021 Environmental Testing Part 2: Test Methods Test Kb: Salt Spray, Alternating (Sodium Chloride Solution)
12. NB/T 10279-2019 'Wet and Hot Environmental Conditions for Transmission and Transformation Equipment'
13. NB/T 10280-2019 'Wet and Hot Environmental Conditions and Technical Requirements for State Monitoring Devices Used in Power Grids'
14. YZ/T 0174-2020 Technical Requirements for Cold Chain Delivery Insulation Box
15. T/CPF 0012-2020 Guidelines for Testing Small Transport Packages for Express Delivery
16. T/CPF 0011-2020 Guidelines for Testing Electrical Transportation Packaging in E-commerce Logistics